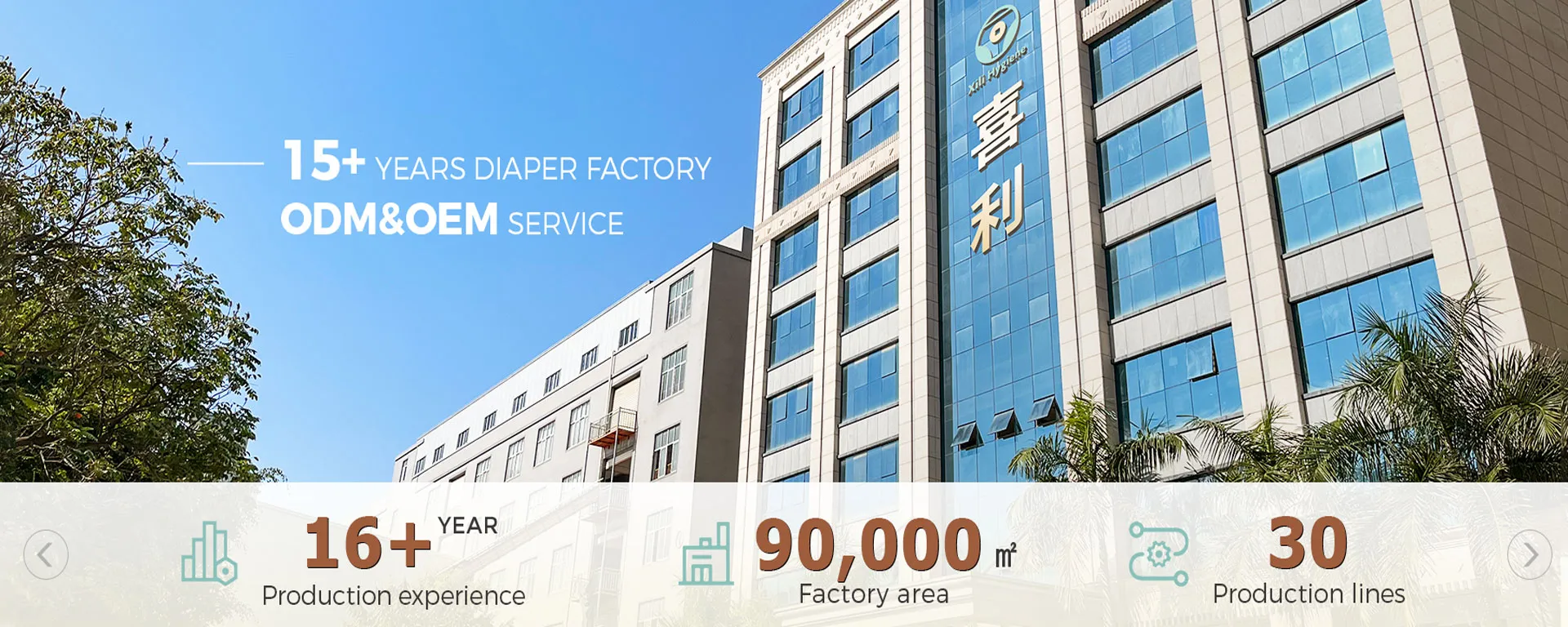
Henkel’s Easyflow®: Revolutionizing Adhesives for Baby Diapers and Sustainable Manufacturing
2025-01-23 22:00
Henkel’s Adhesive Technologies business continues to set new benchmarks in material science and scientific expertise, helping industries gain a competitive edge while advancing their sustainability goals. One of its most groundbreaking innovations, Easyflow®, is redefining hot melt adhesive application in industries such as hygiene products, packaging, and textiles.
For manufacturers in the baby diaper industry, Henkel’s Easyflow® presents a game-changing solution that enhances efficiency, sustainability, and cost-effectiveness. By introducing a patented pressure-sensitive hot melt adhesive in the form of non-sticky micro chubs, this advanced technology facilitates automatic feeding into hot melt tanks, significantly optimizing production lines for baby diapers and other hygiene products.
With the demand for eco-friendly, high-performance baby diapers on the rise, adhesive technology plays a crucial role in improving product quality, reducing waste, and minimizing costs. Henkel’s Easyflow® emerges as a powerful enabler for sustainable baby diaper manufacturing, ensuring strong bonding, leak protection, and enhanced process automation.
How Easyflow® Enhances Baby Diaper Manufacturing
The baby diaper industry relies heavily on high-performance adhesives for:
✅ Secure fastening systems (such as resealable tapes and elastic ears)
✅ Leak-proof barriers to ensure superior protection
✅ Core integrity bonding for better absorption and comfort
Henkel’s Easyflow® hot melt adhesive provides seamless integration into diaper production lines, offering reduced downtime, lower waste generation, and consistent adhesive application. Unlike traditional hot melt adhesives that require manual handling and refilling, Easyflow® micro chubs are designed for auto-feeding systems, allowing manufacturers to improve productivity while reducing material waste.
Key Benefits of Easyflow® for Baby Diaper Production
1. Increased Efficiency with Auto-Feeding Technology
One of the biggest challenges in baby diaper production is the frequent manual refilling of hot melt adhesive tanks, which interrupts operations and reduces efficiency. With Henkel’s Easyflow®, manufacturers can automate adhesive feeding, resulting in:
🕒 Several hours saved per week on manual tank refilling, allowing operators to focus on improving line performance.
⚙️ Fewer production interruptions, reducing downtime and increasing output.
🚀 Higher operational efficiency, leading to better product consistency and quality.
For baby diaper manufacturers producing millions of units per month, these efficiency gains can translate into significant cost savings and higher production capacity.
2. Cost Reduction in Adhesive Application and Maintenance
Traditional hot melt adhesives require frequent maintenance, which increases costs due to clogging, overheating, and residue build-up in adhesive tanks. Easyflow® eliminates these issues with its non-sticky micro chub format, offering:
💰 50% reduction in adhesive-related costs for interventions, maintenance, and spare parts.
⚡ Less downtime caused by clogged adhesive nozzles or inconsistent bonding performance.
🔧 Lower spare part replacement costs, reducing the overall cost of ownership for hot melt equipment.
By switching to Easyflow®, baby diaper manufacturers can achieve higher profitability through lower maintenance costs and enhanced production efficiency.
3. Superior Product Quality and Reduced Waste
In baby diaper production, ensuring consistent adhesive application is crucial for leak protection, comfort, and durability. Easyflow® enables "melt-on-demand" technology, ensuring that the exact amount of adhesive is used without over-application or waste.
🎯 Improved adhesive quality, leading to better bonding, stretchability, and durability of baby diapers.
🛡️ Enhanced leak-proofing, preventing diaper failures and ensuring consumer satisfaction.
With Henkel’s precision adhesive solutions, manufacturers can create high-performance baby diapers that meet strict quality standards while reducing material waste.
Sustainability Advantages of Easyflow® for the Baby Diaper Industry
As the global demand for sustainable hygiene products grows, baby diaper manufacturers are under pressure to reduce their environmental impact. Henkel’s Easyflow® contributes to sustainability in multiple ways:
🌱 Minimized Raw Material Waste – Easyflow® ensures that only the necessary amount of adhesive is melted and used, reducing excess material waste.
♻️ Eco-Friendly Manufacturing – Easyflow® supports sustainable production practices by eliminating unnecessary adhesive waste and disposal costs.
By integrating Easyflow® into baby diaper production, manufacturers can align with sustainability goals while enhancing operational efficiency.
Henkel’s Leadership in Adhesive Innovation for Baby Diapers
Henkel has long been a trusted partner for the baby diaper industry, offering cutting-edge adhesive solutions that enhance product performance and manufacturing efficiency. With a focus on sustainability and advanced material science, Henkel continues to develop next-generation adhesives that:
✅ Improve baby diaper comfort, fit, and durability
✅ Support high-speed manufacturing processes
✅ Enhance leak-proofing and absorbency
As the baby diaper market continues to evolve, Henkel’s Easyflow® positions itself as a transformational technology, helping manufacturers produce high-quality, sustainable, and cost-effective baby diapers.
Get the latest price? We'll respond as soon as possible(within 12 hours)