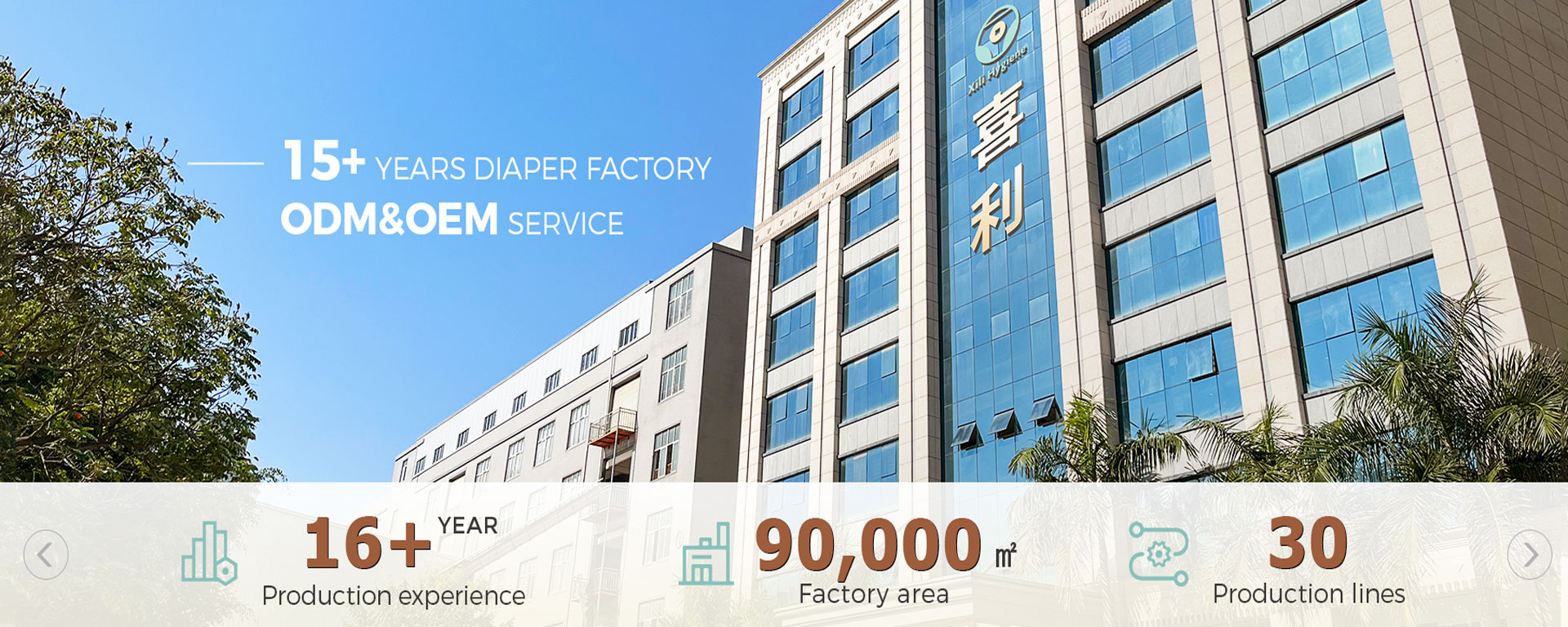
Everything Incontinence How Diapers are Made | Disposable Diaper Overview
2023-08-25 09:58
Now made entirely free of rubber, latex, parabens, pigments, and dyes, today’s diapers can absorb 15x their weight in water with the use of a few genius improvements that have arisen over time, like synthetic polymers and wood pulp fluff that provide maximum absorption and retention capacity that rival the cloth diapers of yesteryear.
Disposable diapers are primarily made up of two major components: an absorbent pad and non-woven fabric sheets. The absorbent pad is composed of a super absorbent polymer (SAP) and fibrous wood pulp material that together form the soft, water-retaining core of the diaper. Super absorbent polymers that are often used in disposable diaper production are a byproduct from other industrial sources, which helps manufacturers to reduce diaper production costs while re-purposing the polymer particles that would otherwise be too refined for use elsewhere. These SAPs are chemical-based products made from acrylic acid derivatives like sodium polyacrylate (most common), potassium acrylate, and alkyl acrylate, which increase the overall absorbance and water retention capacity of the diaper, like a very small sponge in size and function. The minimal size of the polymer particles also helps to effectively reduce the overall size or bulk of the diaper, allowing it to be thinner with less use of wood pulp filling. There are two types of super absorbent polymers that are used for adult disposable diaper production today; one type absorbs greater volumes of liquid with less retention capacity, while the other has greater retention capacity at the cost of lower absorption volume. The specific type of polymer used is ultimately dependent on the individual diaper product being marketed, however, the goal of greater absorption volume is typically the deciding factor in choosing an SAP at this stage.
At the microscopic level, polymer particles appear as ropes or long chemical chains that interact with water molecules and can attach to other polymer particles by “cross-linking.” When multiple polymer chains become cross-linked, a gel network forms that is highly absorbent and is not water-soluble. The strength of this gel network is variable based on the level of cross-linking within the polymer particles yet is an important factor in the polymer’s water-absorbing efficiency. For example, in the event of a cross-linkage that is too strong, the polymer is unable to retain an optimal amount of water within the gel network. If the cross-linkage is not strong enough, however, then the polymer chain can break apart, allowing outer particles to absorb water at a faster rate. When this happens, a gel is formed that prevents additional water from reaching the absorbent pad’s center in a process called “gel blocking.” To prevent this, wood pulp fibers that act as surface cross-links are mixed into the polymer matrix to attract and evenly distribute water molecules throughout the absorbent pad and into the highly absorbent core.
The wood pulp filling or “fluff,” typically sourced from pine trees, is a cellulose product used as the primary absorbent component of the diaper, in combination with the polymer particles to make up the ultra-absorbent pad. The wood pulp’s high fiber-to-weight ratio, short fiber length, and surface tension make it ideal for rapid absorption. Water molecules are drawn, as if by a tiny drinking straw, into the wood pulp’s microscopic empty spaces (called capillaries) found in between the wood fibers. A few additional, but less effective, alternatives to the wood pulp that can also be used for absorbency include air-laid synthetic fibers, cellulose acetate, and polypropylene fibers. Once the liquid has been absorbed by the wood pulp core, the polymer then reacts with the water molecules to form the gel network that retains the liquid within the diaper’s absorbent pad as previously discussed.
At the assembly stage, the wood pulp and polymer particles are vacuum-formed together on a conveyor belt system. Through a series of polymer-fiber applications via pressured sprayers, a cohesive and flattened fluff core is created that can then be cut into diaper-sized pieces. The result is a layered “sandwich” of wood pulp fiber and polymer particles, with the superabsorbent polymer concentrated in the absorbent pad’s center surrounded by the fibrous fluff. Non-woven fabric sheets are then attached to the absorbent pad to give the diaper its “shell” and flexible shape.
While most fabrics are woven together using wool, silk, cotton, or polyester fibers, non-woven materials are generated by various thermal, mechanical, and chemical means using plastic fibers made from polyester, nylon, polypropylene, or polyethylene resins. Non-woven fabrics used for disposable diaper production are made during a dry-laid process known as the “melt-blown” method, where plastic resins such as polypropylene and polyethylene are melted, cooled, and condensed to form permeable and non-permeable sheets for the diaper. The sheets are pressed with heated rollers to bond and flatten the plastic fibers, and then cut to size for the maximum diaper width.
The non-woven fabrics that form the diaper’s top sheet, leak guard, and back sheets are formed separately and differ slightly in their assembly and plastic resin type. The top sheet and “leak guard” layer is made of both hydrophilic and hydrophobic polypropylene fabrics, that allows liquids to pass through the top layer (hydrophilic) while preventing leakage around the absorbent pad and leg cuffs (hydrophobic). Between the top polypropylene sheet and the absorbent core, there can often be a quick-wicking ‘Acquisition and Distribution Layer’ (ADL) made from trough air bond (TAB) non-woven fabric or an aperture sheet of perforated plastic film.
These ADLs can be used in the center of the diaper pad or along the pad’s entire length and are particularly important for thin/ultra-thin diaper types where liquids must rapidly be distributed to the absorbent core and away from potential leakage areas. The additional layer of separation from the wet pad by the ADL also protects the skin where it meets the diaper. Extra components such as lotions, aloe vera, and various oils can also be added to the non-woven top sheet for additional comfort and marketing purposes. The back or bottom sheet of the diaper is made with a hydrophobic, polyethylene film that often includes a thin, “breathable” polypropylene sheet layer.
After the non-woven sheets have been formed, they are wound into large bolts for delivery to the diaper manufacturer, as they are made in a separate facility from the absorbent pad. At the diaper manufacturing site, the non-woven sheets are attached to a large roller that feeds the fabrics separately through the diaper assembly line where they are then fitted to the absorbent pad. The back sheet and absorbent pad are first fed together through a conveyor belt system where they are glued together and then joined by the top sheet that is fed into the system afterward. Stretchy, elastic bands are attached to the back sheet with adhesives and form the flexible leg cuff and waist areas of the diaper. These elastics are usually made from polyester or polyurethane foam, or synthetic rubber materials and can also be used for the diaper’s side panels and fastening zones. Two different types of hot melt adhesives (construction and elastomeric) are the most used methods of joining the diaper’s individual components and are made using mixtures of oils, resins, and tackifiers.
While both types of adhesives are applied to the non-woven fabric, the construction adhesive is used for the diaper’s back sheet, and the elastomeric adhesive is used for the leg and waist elastic areas. These adhesives are applied while in a molten state that eventually cools to form a well-bonded union of the diaper’s components. To hold the diaper in place on the body, fasteners made from Velcro or polypropylene sticker tape are attached to each side of the diaper with an application of adhesive. Once all the components have been joined together, the diaper is cut further to the desired shape, and then packaged for shipment.
Unfortunately, disposable diaper production does not come without its share of byproducts and waste. Non-woven fabric material and polymer particles are both wasted to some degree during the assembly process, however, industry standards work to reduce this by encouraging the optimal use of materials per meter, and with the reclamation of excess wood pulp fibers and polymer particles. The size and distribution of polymer particles in relation to the wood pulp fibers are also a key factor in minimizing waste, by optimizing production strategies to use as little material as possible during manufacture.
Quality control is also taken very seriously for disposable diaper production to ensure that each component is working to its best ability. For example, the diaper’s absorbency is tested using the Demand Wettability or Gravimetric Absorbance standard that measures the diaper’s absorbance under load (AUL). The AUL is based on the total volume of 0.9% saline solution that is absorbed by SAP’s when tested under pressure to simulate a child or adult’s applied weight on the wet diaper. To pass the test, the diaper must absorb 24 ml/g of water or more within 60 minutes. Because the effectiveness of SAP’s is dependent on the presence of electrolytes and considering that urine contains around 0.9% of mineral electrolytes, disposable diapers are tested using a 0.9% saline solution instead of pure water. Another consideration for quality control standards in disposable diaper production is the non-woven fabric’s melting point that must be consistent across each sheet of fabric. Otherwise, the difference in melting points can result in a product that is unsuitable for the wearer.
Get the latest price? We'll respond as soon as possible(within 12 hours)